“A Planet Farms entrano i semi ed escono prodotti confezionati dall'eccellente profilo organolettico e privi di residui di agrofarmaci”, ha dichiarato Travaglini durante il lancio del progetto alla Triennale di Milano. “Nella nostra vertical farm non lasciamo nulla al caso. Controlliamo i fattori fondamentali della produzione, come aria, acqua, luce e terra. E abbiamo coinvolto partner che sono leader nei rispettivi settori”.
Vertical farm, il modo nuovo di produrre cibo
Su AgroNotizie ci siamo occupati varie volte di vertical farm, soprattutto in riferimento agli Stati Uniti, dove questa tecnica di produzione sta prendendo piede. Il concetto di coltivazione indoor è relativamente semplice: slegare la crescita delle piante dall'imprevedibilità della natura, trasferendone la crescita all'interno di strutture chiuse.Le vertical farm sono dei veri e propri impianti produttivi dove le piante (di taglia bassa e ciclo breve) crescono illuminate da luci al led e nutrite grazie alla fertirrigazione. Si usano solitamente idroponica, acquaponica o aeroponica. Nel caso di Planet Farms gli esperti coinvolti nel progetto hanno optato per l'utilizzo di un substrato di torba e di un sistema a flusso-deflusso.
L'atmosfera è controllata in maniera artificiale. Umidità, temperatura e concentrazione di anidride carbonica sono modulati per mettere le piante nella condizione di produrre al meglio.
“Se in natura le colture soffrono dell'imprevedibilità del clima e dell'attacco di insetti e malattie, all'interno del nostro impianto sono protette e dunque possono svilupparsi al meglio”, ha spiegato l'altro fondatore di Planet Farms, Daniele Benatoff, ex Goldman Sachs.
I vantaggi del vertical farming
Ma perché coltivare in un magazzino al chiuso piuttosto che in pieno campo? I vantaggi sono stati ben elencati durante il lancio di Planet Farms che ha visto una partecipazione consistente di addetti ai lavori e curiosi. Prima di tutto le vertical farms possono essere installate ovunque serva, eliminando i costi di logistica e trasporto.L'utilizzo di agrofarmaci diventa superfluo, essendo coltivazioni in cui microrganismi patogeni, insetti e semi di malerbe non possono entrare. Le insalate coltivate sotto le luci al led hanno un sapore eccellente (chi scrive le ha provate e può confermare) e rimangono croccanti anche dopo giorni dalla raccolta, non necessitando di essere lavate prima del confezionamento.
E poi c'è il tema della sostenibilità. Se produrre un chilo di lattuga in pieno campo richiede l'utilizzo di circa 200 litri di acqua, in una vertical farm ne bastano 1,5.
“I nostri prodotti sono buoni, freschi e naturali”, ha spiegato Travaglini, la cui azienda di famiglia produce impianti per l'essiccazione e la stagionatura di salumi e non solo. “Sono buoni perché possiamo usare varietà delicate, che in campo non sopravviverebbero, riscoprendo sapori perduti. Sono freschi perché a poche ora dalla raccolta finiscono sui banchi del supermercato. E sono salutari perché non presentano residui di agrofarmaci e hanno un eccellente profilo nutraceutico”.
Il grande punto di forza dell'indoor farming è quello di poter gestire tutti gli input produttivi per massimizzare qualità e produttività del 'campo'. Ogni stagione è quella perfetta, si potrebbe dire. Nel gestire i fattori chiave Planet Farms si è avvalsa delle migliori aziende su piazza, coinvolgendole nel progetto. Uno dei partner è ad esempio Signify, ex Philips Lighting, che ha fornito un impianto a led capace di emettere le lunghezze d'onda ideali per la crescita delle piante, modulandole a seconda dello stadio fenologico. Della partita è anche Netafim, che invece ha sviluppato tutta la parte di fertirrigazione.
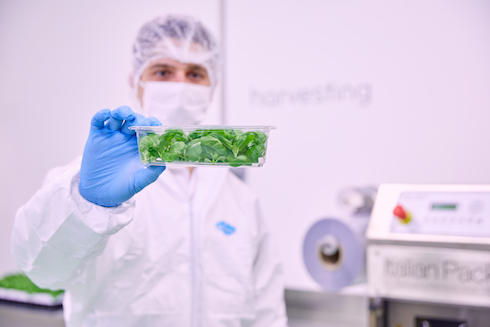
I punti deboli del vertical farming
Gli aspetti negativi riguardano soprattutto i costi di realizzazione dell'impianto. Si parla di milioni di euro per una struttura di novemila metri quadrati dotata delle più moderne tecnologie e che a regime consumerà ingenti quantità di energia per l'illuminazione, la climatizzazione e l'operatività degli impianti. Energia che sarà fornita da RePower, provider energetico e partner del progetto.Costi di avvio estremamente alti dunque, ma a Planet Farms non si fanno scoraggiare: sono sicuri che il prezzo della confezione sullo scaffale non sarà difforme da quello dei prodotti da agricoltura convenzionale, o forse biologica. Insomma, costi di produzione maggiori, ma nessuna diseconomia di filiera.
La visione di un mondo diverso
Planet Farms è un progetto ambizioso, frutto di una visione e un dolore personali. Quelli di Luca Travaglini che nel novembre 2015 è stato colpito da un male tremendo che ne ha messo a repentaglio la vita.“Quando ne sono uscito ho sentito la necessità di dare una svolta alla mia vita e quasi per caso mi sono imbattuto in un articolo che parlava di coltivazioni verticali”, spiega Travaglini. “Mi è scattata una scintilla in testa e ho passato gli ultimi quattro anni e mezzo a viaggiare e studiare per realizzare in Italia il sogno di una vertical farm sostenibile”.
Le sfide del vertical faming
L'idea di slegare la coltivazione di una pianta dalla variabilità e imprevedibilità della natura è affascinate, ma rappresenta una sfida enorme. Basti pensare all'associazione pianta-batteri, che rende possibile la crescita dei vegetali. Il microbioma, l'insieme cioè dei microrganismi che vivono sulla e dentro la pianta, è essenziale per la sopravvivenza della stessa, contribuendo alla nutrizione e al metabolismo della stessa. All'interno di una coltivazione verticale però tutto deve essere sterilizzato, per evitare che si sviluppino microganismi patogeni. La torba viene dunque attentamente controllata, l'aria filtrata e l'acqua sterilizzata con raggi ultravioletti.Per evitare contaminazioni tutto il processo è meccanizzato. Una macchina si occupa del riempimento delle vasche con il substrato, un'altra posizione i semi. Nastri trasportatori e carrelli elevatori movimentano le vasche dentro e fuori le camere di germinazione prima, di crescita poi. Anche il taglio e il confezionamento è automatizzato.
“Quando il consumatore apre la confezione esso è il primo a toccare le foglie di insalata”, ha dichiarato orgoglioso Travaglini.