Lo stabilimento Diachem di Caravaggio, ora anche nuova sede del Gruppo, rappresenta un case-history degno di studio, grazie all'organizzazione razionale dei processi produttivi ed al rispetto dei più moderni requisiti in materia di sicurezza.
Innanzitutto, la gestione dei prodotti ad azione erbicida è tenuta rigorosamente separata da quella dei non erbicidi, al fine di evitare possibili contaminazioni fra prodotti.
Non è infatti per caso che oltre a formulare i prodotti Diachem, lo stabilimento operi anche conto terzi per diverse aziende del settore, le quali si affidano alla società bergamasca per la produzione e il confezionamento dei propri formulati.
Quanto a superfici, lo stabilimento occupa 38 mila metri quadri di cui circa 15 mila coperti. L'insediamento si pone al centro di terreni di proprietà della famiglia Dubbini, proprietaria di Diachem, e rappresenta anche uno dei quattro depositi di cui la società dispone in Italia.
All'interno del complesso lavorano circa 90 persone, di cui una settantina nello stabilimento e circa venti negli uffici.
Anche i processi per la produzione dei formulati solidi avvengono in edifici differenti da quelli in cui sono prodotti i liquidi.
Un'organizzazione del lavoro che ottimizza quindi tempo ed energia, mantenendo anche un ottimo livello di sicurezza e di tracciabilità dei processi.
Di seguito viene riportato un reportage fotografico che mette in evidenza i diversi punti chiave dello stabilimento.
Foto 1: il processo di formulazione dei prodotti solidi beneficia di un efficiente sistema di abbattimento polveri posto all'esterno dell'edificio. Questo evita dispersioni nell'ambiente dei residui di lavorazione
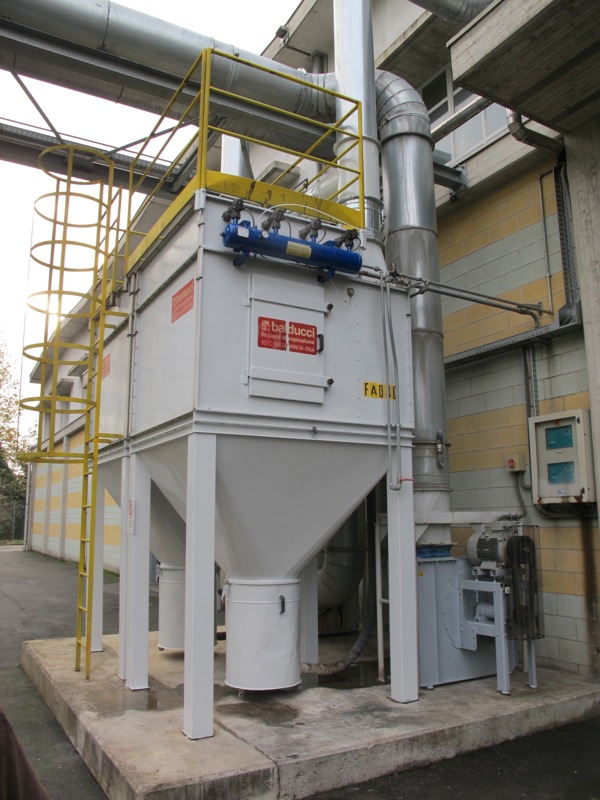
Foto 2: la robottizzazione dei processi ottimizza tempi e precisione del lavoro. In questo caso è raffigurato un robot per la realizzazione dei pallet per il trasporto dei formulati solidi.
Foto 3: il modellino in scala riportato nella foto raffigura un mulino dedicato al processo di produzione dei formulati "Flow". Le sfere di Zirconio sono estremamente dure e resistenti e permettono la frammentazione spinta delle particelle solide. Ciò permette una migliore emulsione di queste con la componente liquida rappresentata dall'acqua. Il risultato è un formulato stabile nel tempo e che non mostra fenomeni di separazione delle fasi d'immagazzinamento.
Foto 4: l'impianto di produzione dei "Flow" è in grado di operare anche a 800 kg/h. Nel caso dei prodotti a base Zolfo sono necessari due passaggi: il primo a 800 kg/h, il secondo a circa 600 kg/h, necessario per raffinare ulteriormente la micronizzazione delle particelle solide.
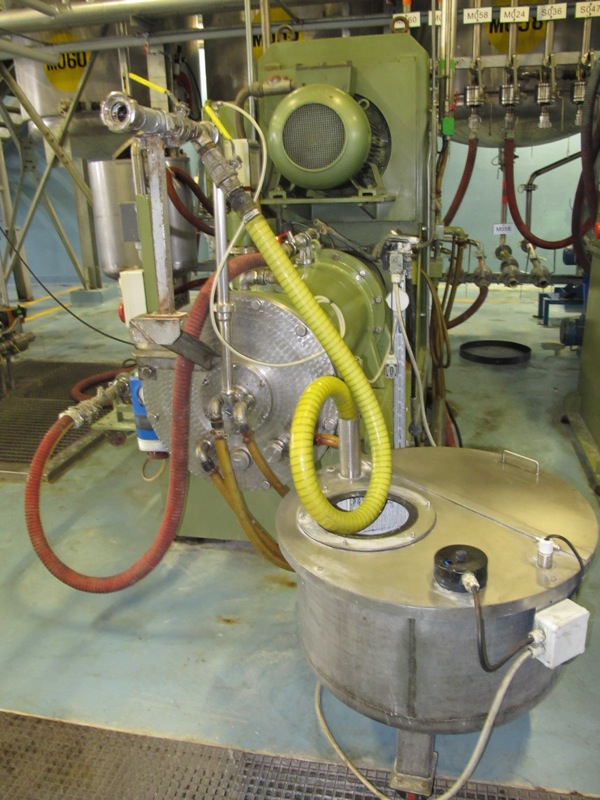
Foto 5: il risultato dei processi di produzione è un formulato "Flow" omogeneo e stabile nel tempo.
Foto 6: il processo di imbottigliamento è totalmente automatizzato e conta su un sistema di pesatura elettronica per fissare l'arresto delle procedure di riempimento delle singole bottiglie.
Foto 7: anche il processo di etichettatura risulta automatizzato e di estrema precisione.
Foto 8: l'impianto automatizzato di imballaggio consente in pochi secondi di confezionare nell'apposita scatola 10 bottiglie in soli due prelievi da 5 pezzi ciascuno.
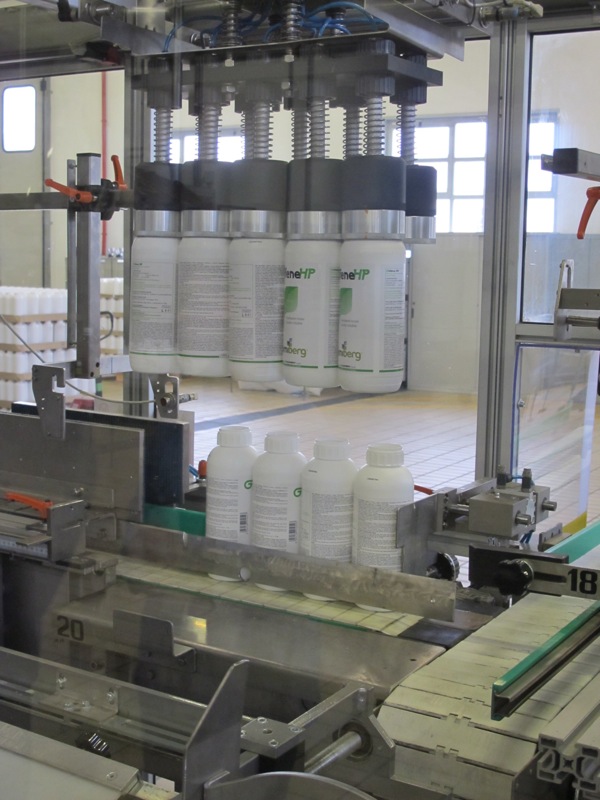
Foto 9: i processi di imbottigliamento sono analoghi a quelli sopra descritti anche per quanto riguarda le confezioni da cinque e da dieci litri.
Foto 10: i cartoni contenenti le bottiglie dei formulati liquidi vengono anch'essi movimentati e impilati grazie all'ausilio di moderni robot gestiti da software dedicati.
Foto 11: il magazzino è organizzato in modo moderno e razionale e permette di tracciare ogni singolo collo grazie a un sistema di codici a barre. L'operatore che scarica o carica un nuovo collo non deve far altro che utilizzare l'apposita pistola di lettura codice e il sistema centralizzato lo classifica e lo posiziona. Quando il collo viene rimosso per la spedizione un'analoga lettura scarica il codice e impedisce che lo stesso collo possa essere contato due volte.
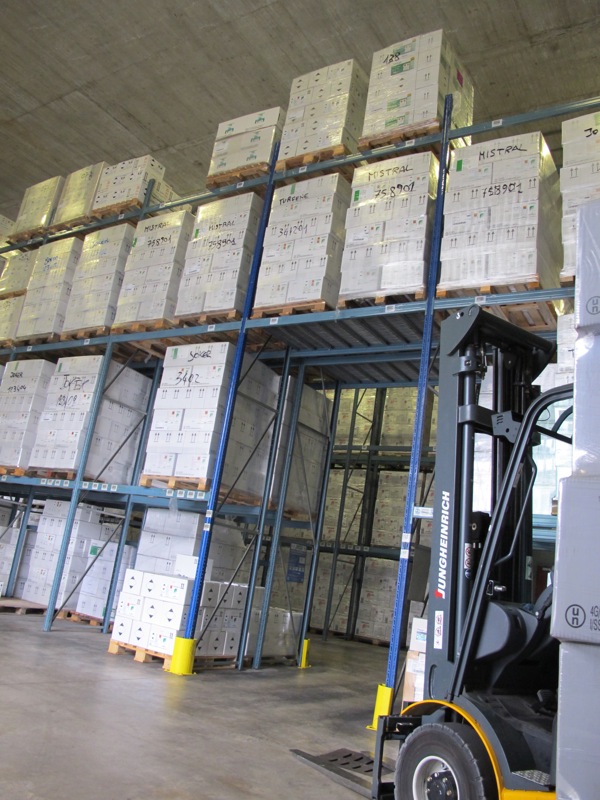
Foto 12: le porte del magazzino sono controllate da elettrocalamite collegate al sistema anti incendio. In caso di pericolo le porte si chiudono automaticamente e il locale viene invaso fino al soffitto da un'apposita schiuma ignifuga.
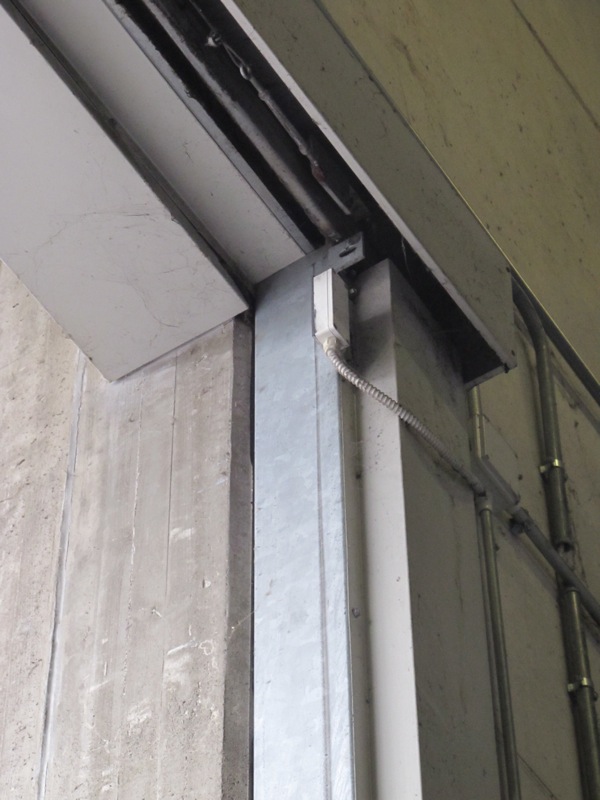
Foto 13: il pavimento dei magazzini è concepito per raccogliere all'interno i liquidi eventualmente formatisi a seguito di uno sversamento, per poi convogliarli verso appositi tombini che li trasferiscono a vasche sotterranee di raccolta. L'impatto per l'ambiente diviene in tal modo nullo anche in caso di incidente.
Foto 14: per motivi di sicurezza il locale di immagazzinamento dei solventi è tenuto separato da tutti gli altri edifici. Apposite linee trasferiscono i diversi solventi verso le relative destinazioni.
Foto 15: dispositivo di sicurezza per scongiurare l'emissione di scariche elettrostatiche durante il trasferimento dei solventi dalle autobotti al magazzino. Se la pinza di messa a terra non è collegata all'autobotte non può partire il processo di trasferimento dei solventi
Foto 16: l'impianto Diachem conta anche su cinque unità di pannelli solari a "girasole", grazie alla quale i pannelli ruotano durante il giorno seguendo la migliore posizione rispetto al sole. Dall'impianto Diachem ricava 200 Kwh di picco, capace di soddisfare circa il 25% del fabbisogno energetico dell'insediamento. Anche dal punto di vista delle emissioni di CO2 Diachem si pone quindi all'avanguardia
Foto 17: Cerimonia di inaugurazione della nuova sede. Al taglio del nastro tutte e tre le generazioni della famiglia Dubbini
© AgroNotizie - riproduzione riservata
Fonte: Chimiberg - marchio di Diachem S.p.A.
Autore: Donatello Sandroni