Per diverse realtà produttive la ripartenza è avvenuta già da un paio di settimane e chi più, chi meno, si rincorre il tempo perduto.
"La produzione a Breganze è ripartita il 4 maggio - fa sapere Paolo Andreone product e price manager del comparto harvesting Eme di AGCO - e grazie al lavoro fatto sin dalle prime avvisaglie di contagio in febbraio, ci siamo già portati a livelli produttivi prossimi al 100% della capacità dello stabilimento". A riprova, il 6 maggio scorso sono uscite le prime macchine dalla linea di produzione.
Una task force per la ripresa
Il segreto di Breganze è stato mettere in campo un'organizzazione lungimirante per arrivare il più efficienti possibile al momento della riattivazione. "Abbiamo fatto un lavoro veramente fine" chiarisce Andreone. "Di fronte alla chiusura di uno stabilimento produttivo, il vero problema è la ripartenza. In particolare laddove il processo produttivo dipende dai fornitori esterni".Un attento lavoro di monitoraggio dei fornitori ha permesso di non arrivare mai ad uno stop totale della produzione di componenti. Nonostante l'arresto delle linee di montaggio, mantenere in vita la catena di approvvigionamento di componenti (provenienti dall'Italia, dall'estero ma anche prodotti internamente) è stata la chiave per ripartire senza accumulare eccessivo ritardo sulle consegne.
"Non abbiamo, nella stragrande maggioranza dei casi, dovuto sostituire i fornitori. Al massimo, abbiamo temporaneamente portato all'interno qualche piccola produzione" sottolinea il manager.
Fin da subito nel Competence Centre AGCO Spa una task force appositamente istituita si è occupata di definire le misure di sicurezza e protezione dei dipendenti e le attività necessarie a garantire il costante servizio ai clienti.
"Abbiamo dotato i dipendenti degli ausili di protezione, predisposto le operazioni di sanificazione, le distanze di sicurezza, abolito trasferte e riunioni" spiega Simonetta Lambrocco Eme marketing external communication & services manager AGCO. "Abbiamo anche installato speciali maniglie apribili senza contatto con le mani. Dal 16 marzo, alla partenza del blocco totale abbiamo chiuso mantenendo però attive, con personale ridotto e in deroga al decreto ministeriale con l'accordo della prefettura, le attività che non potevano prescindere dalla presenza fisica come il servizio fornitura ricambi, l'accettazione e i controlli qualità. Il resto è stato gestito in home working che stiamo continuando a mantenere dove possibile".
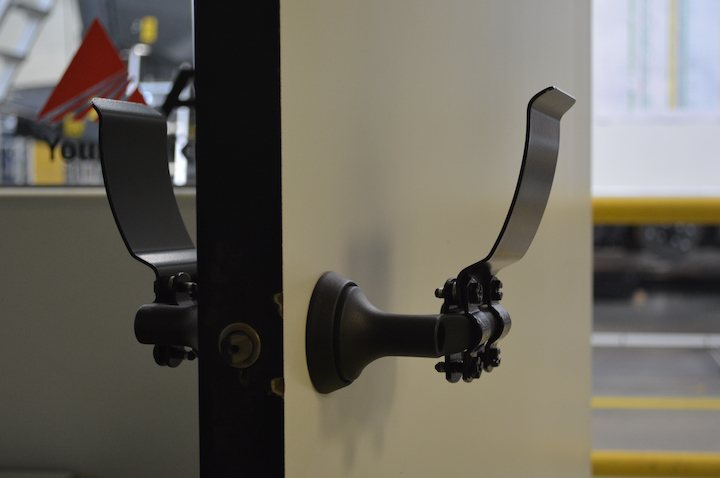
Maniglie con apertura facilitata, che evitano il contatto con le mani, installate negli stabilimenti AGCO Europe
Ideal, non cambia strategia
La possibilità di portare a termine le consegne di ordini arrivati prima della chiusura ha ridotto gli stock che ora devono essere ripristinati. "Abbiamo un programma di recupero che si avvantaggia del tempo che ci separa dalla stagione della raccolta. Con un incremento della cadenza produttiva - possibile grazie al flusso componenti manutenuto costante - e gestendo le criticità tramite assegnazione di una priorità di consegna macchina per macchina, riusciremo a ridurre il gap" afferma Andreone.Confermata dunque la piena ripresa della produzione, tanto che alcuni esemplari di Ideal sono già usciti dalle linee di montaggio dello stabilimento di Breganze nella settimana del 6 maggio 2020.
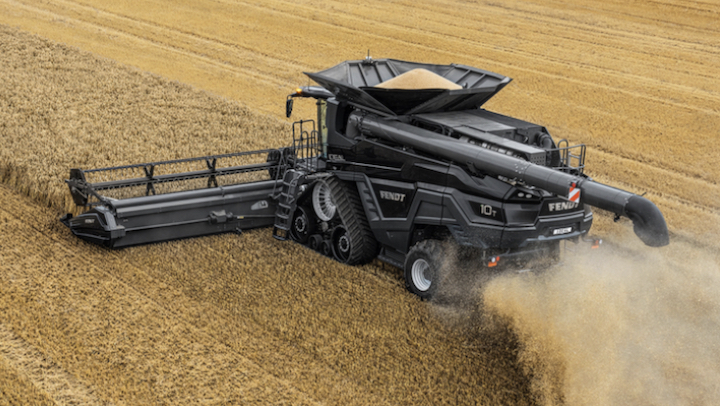
Ideal 10T in campo
"I volumi di produzione della Gamma Ideal da qui a luglio, sono confermati - dichiara Andreone - e andranno a coprire le richieste della stagione 2020 con una produzione di circa duecento macchine prodotte a Breganze e destinate al mercato europeo, cui si aggiunge un rilevante contingente di macchine Ideal per il mercato nordamericano". Invariato anche l'obiettivo di medio termine di 2.500 macchine sui mercati Eme, Nafta e Latam, dichiarato in occasione del lancio della Gamma Ideal nel 2017.
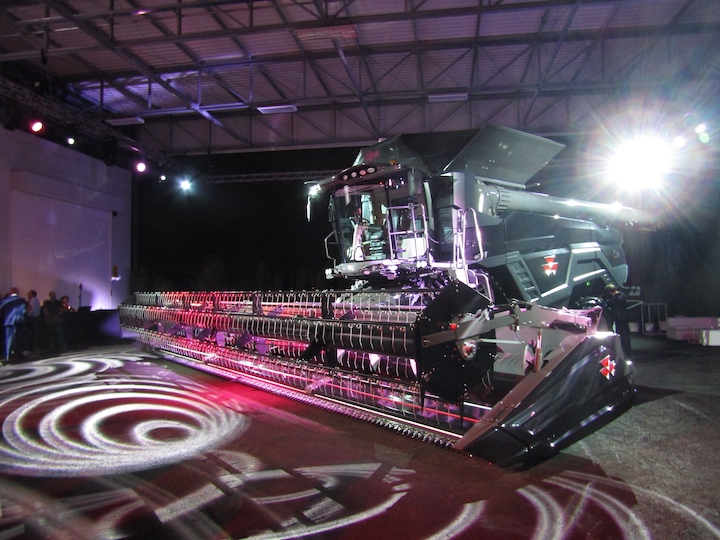
Ideal 9 nello stabilimento di Breganze durante il lancio alla stampa
Con una capacità produttiva di mille macchine anno, il Gold Harvesting Competence Centre di Breganze si è organizzato per riprendere la produzione nel minor tempo possibile, recuperando i ritardi dovuti alla chiusura causata dal Covid-19, con obiettivo di soddisfare le esigenze dei suoi clienti nelle diverse aree del mondo.
"Sarà anche la stagione a definire i volumi futuri", spiega Andreone che aggiunge, "la strategia di Ideal sta seguendo tutte le milestone prefissate e dal 2021 avremo sviluppi di prodotto ma anche importanti novità in quanto a capacità e modalità produttiva dello stabilimento di Breganze. Abbiamo tante idee nel cassetto e siamo attivi su progetti futuri di Ideal a tutti i livelli".